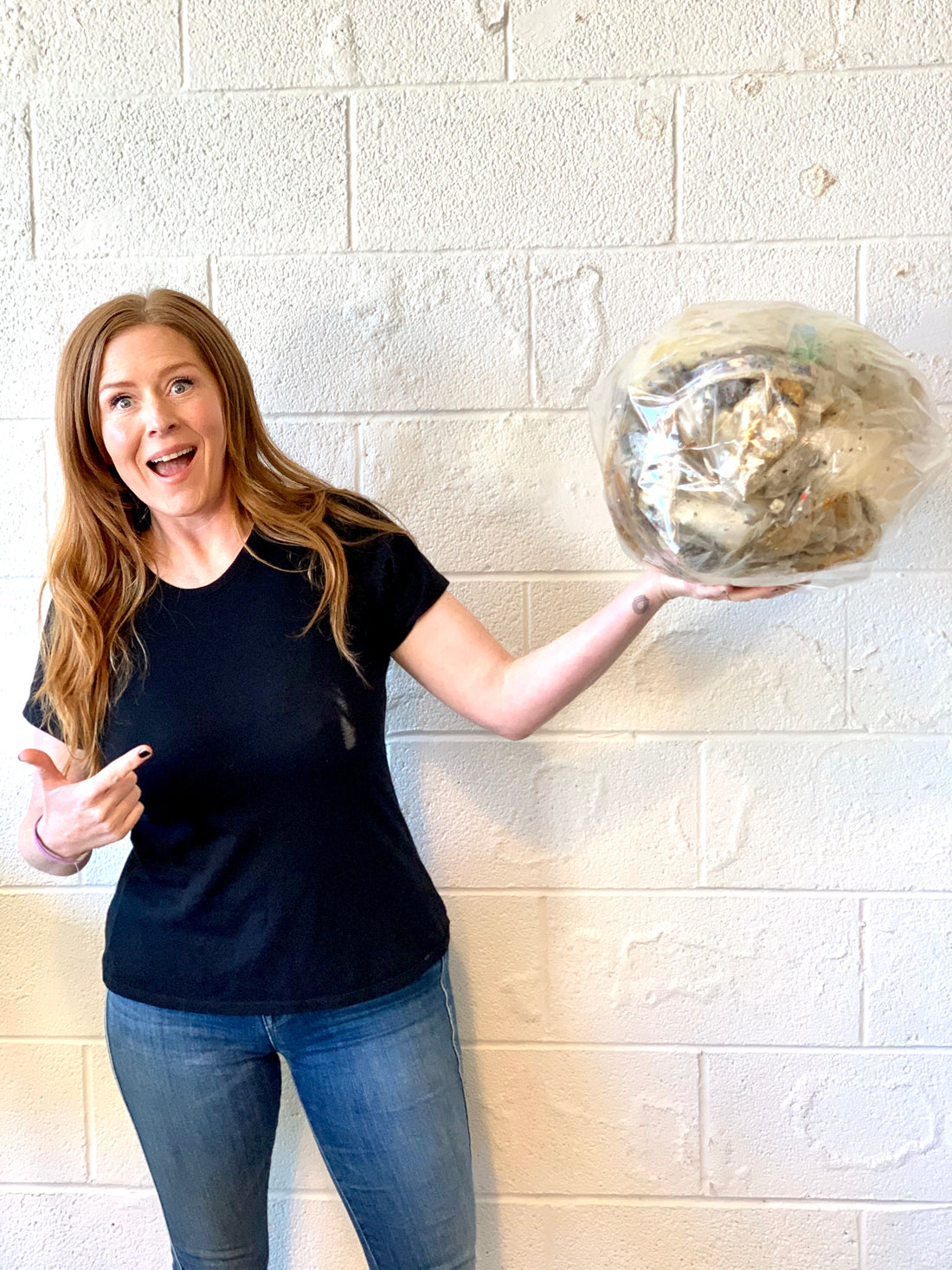
One Year of Trash: Fillaree's First Annual Waste Audit Sends Just 8 Pounds to the Landfill
In 2019, Fillaree partnered with Gather Green, a Durham-based Waste Recovery consulting company that helps businesses divert waste through creative reuse. Here’s what we learned.
In the five years we’ve been in operation, Fillaree has always remained a zero waste business. But did you know that even zero waste (also called “zero landfill”) businesses still produce some level of waste? Despite the different categorizations among communities and businesses, a Zero Waste Business is generally and more technically speaking "virtually zero waste" in that it achieves a landfill diversion rate of around 98 percent or more, while most are considered "landfill diverted" if they achieve between 75 and 80 percent diversion. Those materials diverted are typically either recycled, reused, or composted. In a true zero waste, circular economy, any potential trash generated from products are designed to return back to the manufacturer—much like how our Refiller Subscriber Program functions.
Full disclosure: It’s impossible to be 100 percent zero waste—though we certainly try to get as close as possible! But even though we’re a small, sustainable operation that makes clean, all-natural products, we’re still faced with the same challenges as any business when considering how we might produce less trash. Since transparency is one of our core values, we conducted our first-ever trash audit for 2019 so that we could discover just how much trash we were producing, and get even more creative about how we could generate less and reuse more.
What is a trash audit?

A trash or waste audit is an industrial term for assessing the amount of waste a person or business has generated over a period of time. Since an audit is typically a standard, one-time event that provides limited information and is devoid of solution and strategy, we were really excited when we discovered Gather Green, a green waste management company right here in Durham. Started by Bryce Northington in 2017, Gather Green helps businesses divert waste that’s often harder to recycle and/or reuse. Through Bryce’s unique “waste discovery” process, she looked at every piece of trash produced by Fillaree and evaluated its potential for reuse.
We think the amount of pollution and waste generated by a midsize company is staggering. If the average person produces four pounds of trash per day, we estimate that a small business with a dozen employees could generate at least 20 pounds of trash per day—and about 7,500 pounds of trash per year! Imagine what could happen if more businesses around the country and beyond actually paid attention to how much trash they were producing? We believe that businesses of any size have a responsibility to assess their carbon footprint, especially here in the Bull City. There’s no landfill in Durham—the closest one is 90 miles away in Sampson County and will likely be full within the next 10 years.
Partnering with Gather Green gave us the opportunity to measure exactly how much trash we were sending to the landfill, and it was really important for us to share these findings with our like-minded community. We are pleased to report that since starting our year-long waste audit on January 7, 2019, we managed to produce just eight pounds of trash for an entire year. That's 93 percent less than the average business! And we couldn’t have done it without Gather Green’s innovative reuse and diversion strategies.
In 2019, Bryce visited our soap factory once a month to evaluate our progress, collect our trash for potential reuse, and offer better solutions so that we could produce less waste. Bryce aims to divert waste from all waste streams, including recycling and TerraCycle which spends a ton of energy remaking materials that are still potentially useful. She considers how to give items a second life that use less energy, such as repurposing materials for local artists to create new products like bound books and journals, or by donating to the Durham Scrap Exchange, a creative arts reuse center.
With Gather Green’s help, we made a number of shifts to our product design like switching to compostable labels and even swapping plastic stickers for screen printed bottles. Instead of putting our plastic film in the trash, Bryce took it to a specific place where it was recycled, and sent items like water filters back to the manufacturer. But we’re most excited about in 2020, is Gather Green’s new partnership with Jeffrey Woobenhurst of Fumble Labs, who is building 3D printers that remold 3D printed filament from shredded plastic. Soon, Gather Green will recover all of Fillaree’s plastic waste to go directly to this cutting edge new project and give it a second life.
Even still, there’s always going to be that eight pounds of trash. There will inevitably be that one item that has nowhere to go, like the insulated space blanket we used to wrap our soap tank that was so caked and corroded with soap and sludge that we had no choice but to send it to the landfill. But we do take pride in knowing that the blanket accounted for six of our eight total pounds.
Based on our key findings, here are five things
we learned from our first-ever trash audit.
1. We discovered exactly how much trash we were creating!
In 2019, Fillaree successfully diverted 3,617 pounds of waste from the landfill. In total, we created about 3,625 pounds of waste. Of that, we recycled 2,771 pounds; reused, repurposed, or composted 845 pounds; and managed to send just eight pounds to the landfill (six pounds of which was that pesky electric space blanket!). In order to obtain these figures that made us really proud, we had to become a lot more conscious about what we were recycling, more mindful about the products and ingredients we were purchasing, and a lot more creative about what we were doing with what would have otherwise been trash.
2. We reevaluated how we were labeling our bottles.
For the past five years, the stickers on our reusable bottles were derived from glossy sticker release lining paper made from silicone that cannot be recycled. Sure, there are commercial industrial recycling companies that exist that repurpose this material into plastic bags, but we’d need two tons of release liner paper in order to qualify—and our small business simply does not produce that level of volume (not yet anyway!). Gather Green was able to take some of our plastic film and repurpose it to local stores that used it for cushioning packaged products instead of bubble wrap, but still, we needed a more long term solution that wouldn’t produce any trash at all. We are pleased to announce that by 2021, all of our bottles will be screen printed. We’ve already tested this out on our new Refillable Condensed Soap, and are launching a Kickstarter in February 2020, to bring this exciting new product to market. (Stay tuned for more!)
3. We reassessed our plastic coconut oil bags.
We use a ton of coconut oil for our products which means we need to buy in bulk. And up until our trash audit, we were using these large plastic wrapped coconut oil bags that were so saturated in residual coconut oil that they couldn’t be recycled. The bags alone were an extra 40 pounds of trash! We tried using big drums of coconut oil, but they were so heavy that it made soapmaking nearly impossible, not to mention, incredibly expensive to ship. Since Gather Green also helps businesses protect their bottom line and keep their revenue streams flowing, we knew that the drum just wasn’t going to work for us in the long term. We had to get creative, so we took it a step further. We decided to decontaminate the bags so they could be recycled, since any soiled items that go into the blue bins will still end up in the landfill. Our next solution involved boiling the bags for a few hours until the residual coconut oil could be released and then composted, and the bags cleaned and reused. This did the trick!
4. We made waste diversion integral to our core company culture.
It became clear from the beginning of our trash audit that we needed every employee at Fillaree on board with our zero waste philosophy. That meant bringing your own lunch in reusable containers and not leaving any trash behind. It meant that our relationships with our vendors needed to follow a similar accord. Even Gather Green wouldn’t set up a Waste Recovery Program at a businesses without knowing that the staff could be onboarded and trained as part of this ethos. Fillaree’s Waste Recovery Station was actually a pilot program for Gather Green, and a successful one at that! Each one of our hardworking employees happily adheres to certain zero waste standards that involve a little extra time, effort, and thoughtfulness—which may seem unusual to some. But for our team, it’s part of a new normal that gets us really excited in knowing that we’re each doing our part to reduce our environmental impact and remain transparent with our consumers.
5. We realized that diverting waste is a full-time job.
Our new creative reuse strategies would not have been possible without Gather Green’s services. I’ve attempted to keep track of my trash and perform an audit myself in the past, but as an owner of a small business and a mother of two, I just did not have the time to sort through everything myself. There’s a great need for services like Gather Green to help individuals and businesses actually pull this off! It takes a lot of time and expertise and sort through each piece of trash and consider where it might be repurposed. Bryce says she encounters this problem often with busy business owners, which is why she’s so committed to her cause. It’s not just about sorting your trash and recycling—it’s about shifting your entire outlook and perception about what trash even is and has the potential to become.